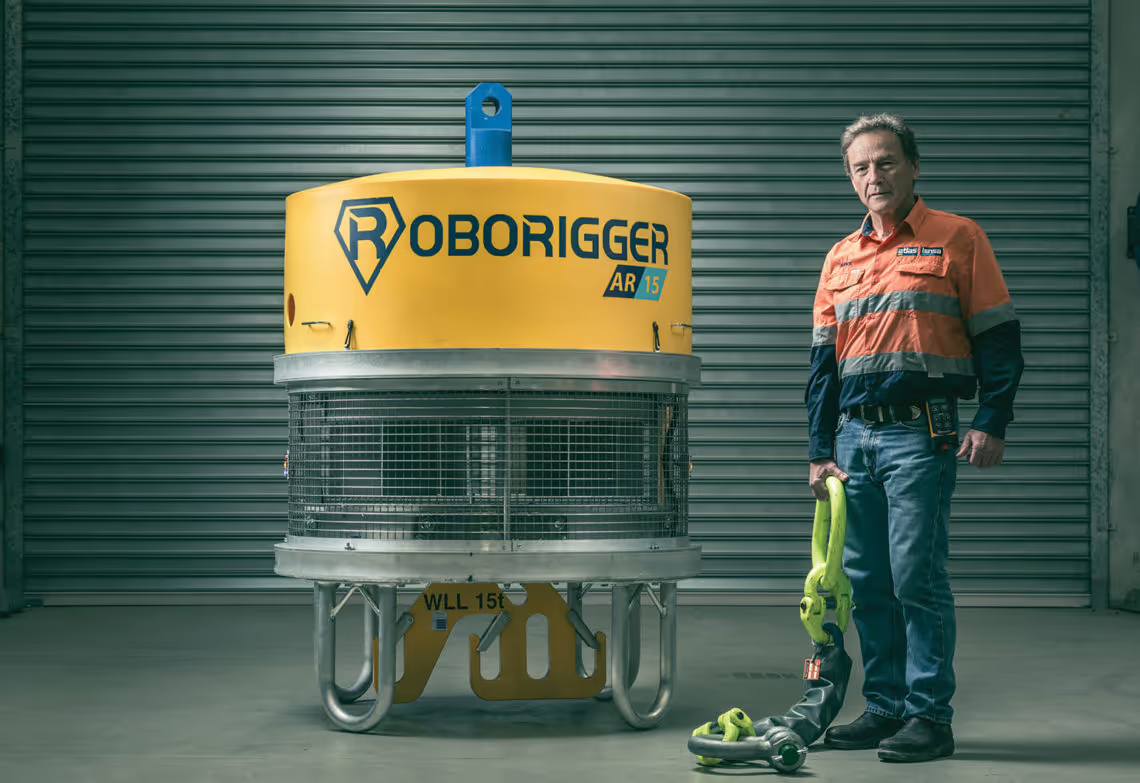
Investment Notes: Roborigger
We’ve invested $5m in an innovation which promises to make worksites safer.
Blackbird has made an investment of $5M into Perth-based robotics start-up Roborigger, a wireless load controlling system which uses gyroscopic and inertial forces to accurately rotate and orient crane loads.
Currently, this job is done manually by ‘dogmen’ or ‘riggers,’ who attach ropes to the load, often standing under it, to move and steady them into the correct orientation. It’s a necessary but dangerous process. For more complex situations, such as delivering a load through a narrow passageway or fitting large prefabricated components, manual rigging is a challenging undertaking.
This job fits squarely into those dirty, dangerous and dull ones that we love seeing robots change for the better.
Dogmen!
Cranes are a significant source of injury and death on site. There are on average three deaths and hundreds of injuries involving cranes in Australia each year. Incidents shut down operations for at least half a day, which results in delays, costing between $50k to $100k/day on a big construction site. Manual rigging is also subject to the natural elements. Depending on the site and activity, when the wind reaches above12 knots per hour (a nice steady breeze), crane operations with large loads are curtailed or stopped altogether — causing more financial ramifications.
Roborigger solves these problems by adding an inertial flywheel device — sitting between the crane hook and the load — that uses accelerometers and software to orientate and keep it steady. It is currently available in three models with lifting capacities of 10, 15 and 20 35 tonnes, with a 50-tonne model currently being built at their Perth factory.
Using a mobile device, the aim of Roborigger is not to entirely replace the riggers, rather make their job far more efficient and safer.
Roboriggers magic lies in reducing the unnecessary danger for riggers by removing the need for human involvement, or as the AFR put it in their recent write up it will “stop cranes killing people.”
This is a product that has already inspired delight for those who work in the area and could prompt strong word-of-mouth distribution. Regardless of whether you’re in construction or not, seeing the Roborigger in action is an impressive sight.
The Founder
At the heart of every great company is a great founder. Derick Markwell, Roboriggers founder personifies this statement. His eyes light up when discussing flywheels, torque, and control systems. Derick brings to the table strong experience in mining and construction engineering with infectious salt-of-the-earth ambition. Roborigger is his third venture. Previously he founded two engineering firms which built oil and gas drilling components. Tensa, Derick’s still operational engineering business — which builds machinery for oil and gas — was the spark for the idea of Roborigger.
Roborigger's current projects include the Adelaide Casino, a car dumper being constructed by Monadelphous for a Fortescue mine in the Pilbara, and was previously used a demolition site on the corner of George and King Street in the Sydney central business district. There are several trial agreements signed from Japanese construction companies, meaning it has truly global potential.
We are excited to be joining the Roborigger journey!