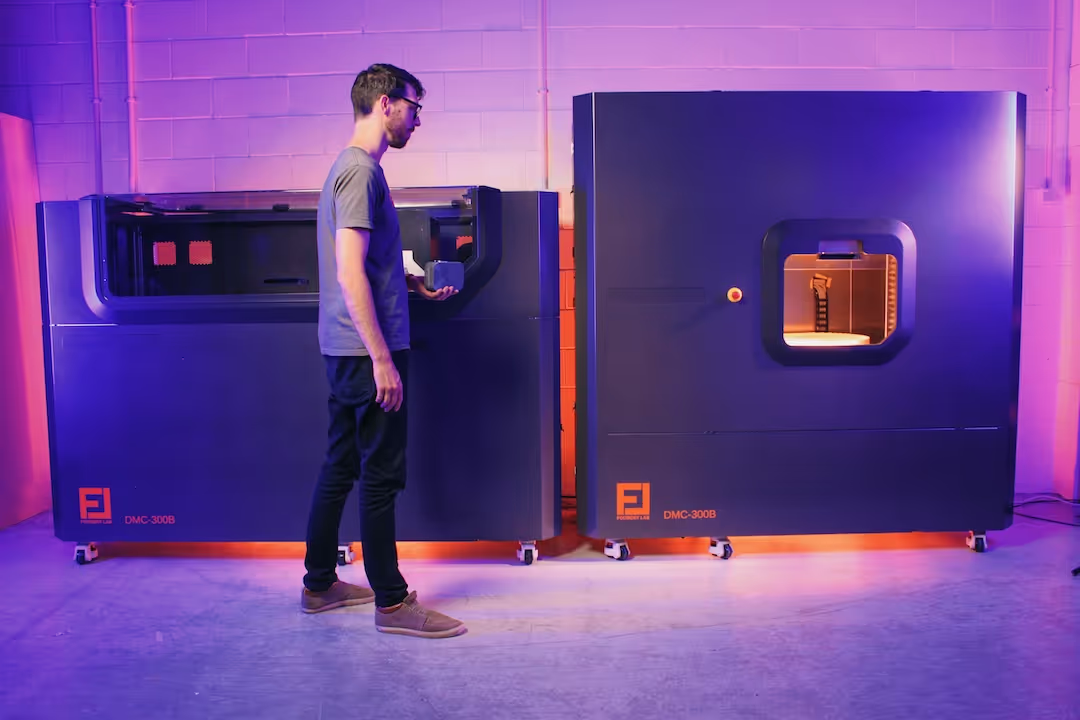
Investment Notes: Foundry Lab
We’re thrilled to have led the Series A round into Foundry Lab, an Aotearoa startup pioneering digital metal casting (DMC) to create functional metal parts in less than a day.
Metal-Melting Microwaves
Foundry Lab is taking a very modern approach to the millennia-old tradition of metal casting, focussing initially on prototyping and short-run cast metal parts. The CEO and Founder, David Moodie, is on a mission to make “metal casting as easy as a microwave dinner.”
The company’s approach is to heat up 3D-printed moulds containing metal ingots in a microwave roughly the size of a small wardrobe to temperatures at which the metal will melt into the desired negative impression. Once the metal has melted into the cast, the microwave blasts the mould with cold air to ‘set’ the metal and then the mould is removed, leaving the solid part.
There are a few aspects to the system:
- 3D printer - that prints the ceramic moulds;
- Microwave - that heats up the moulds to the melting point of the metal being cast and also can blast cool air once the casting is complete;
- Consumables for the 3D printer - a novel, ceramic-like powder that is able to withstand the high temperature in the microwave, plus an adhesive.
- Software that computationally generates instructions for the 3D printer to print the moulds from CAD files.
- The value proposition is CAD file to physical, cast metal part in 4-8 hours, rather than 3 to 8 weeks if sent to a foundry.
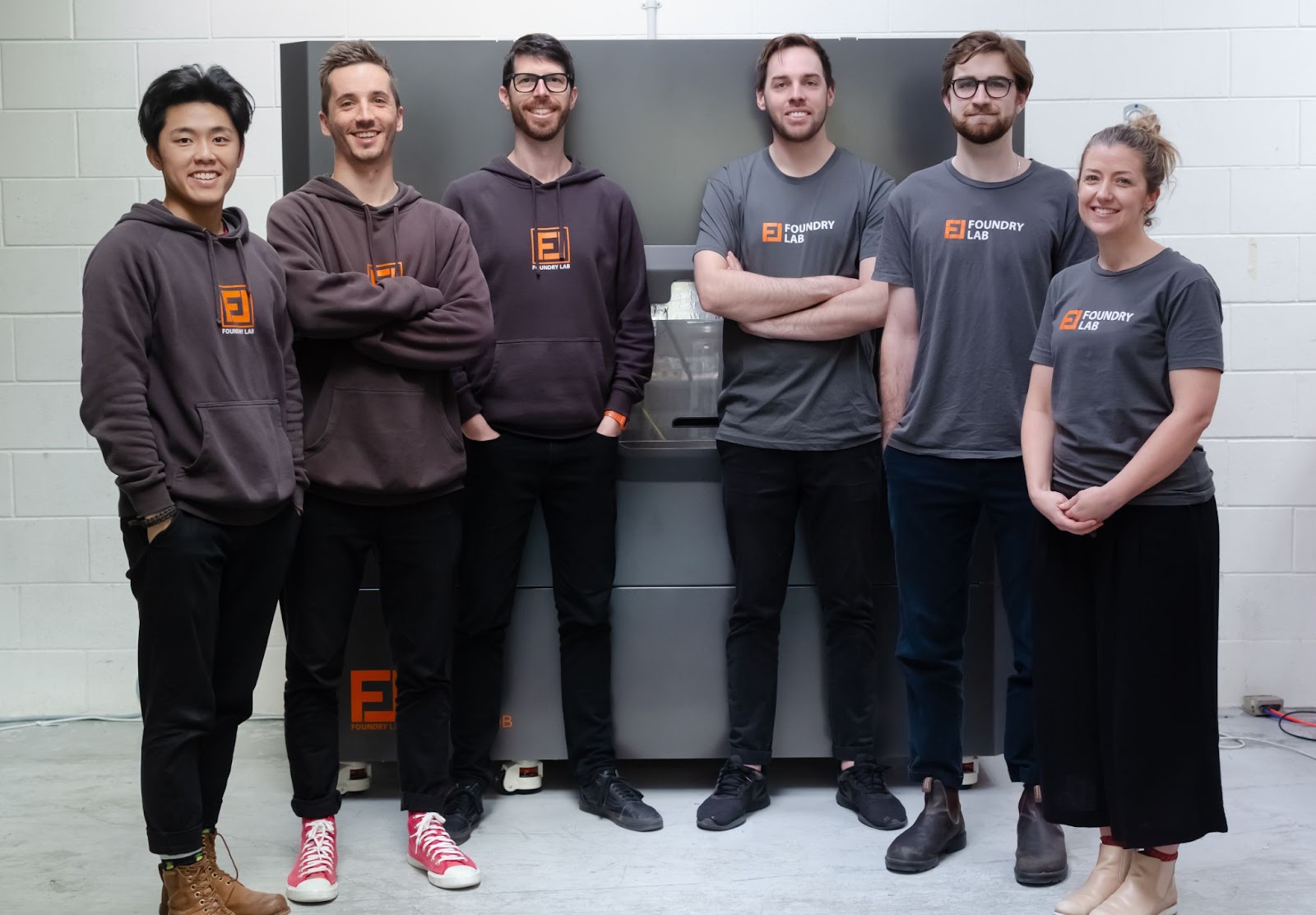
The CEO and Founder of Foundry Lab is David Moodie, an industrial designer of 15 years and a quintessential example of the ‘thinking from first principles’ Kiwi deep tech founder that I have come to know and love.
He discovered the limitations of 3D printing metal while developing new products for clients as part of his industrial design consultancy. Although 3D metal printing is faster than casting, it does not have the physical qualities of cast metal. This matters when you’re producing something that requires functional testing and/or is part of a regulated supply chain.
Bothered by the paradox of using large, expensive, mass production techniques like metal casting in a foundry to make tiny runs of products, he started researching alternatives. Through lots of trial and error, David eventually started hacking away on home microwave ovens and arrived at a proof of concept. Today, he and his team have successfully cast automotive brake shoes from CAD files to cast aluminium parts in less than 8 hours.
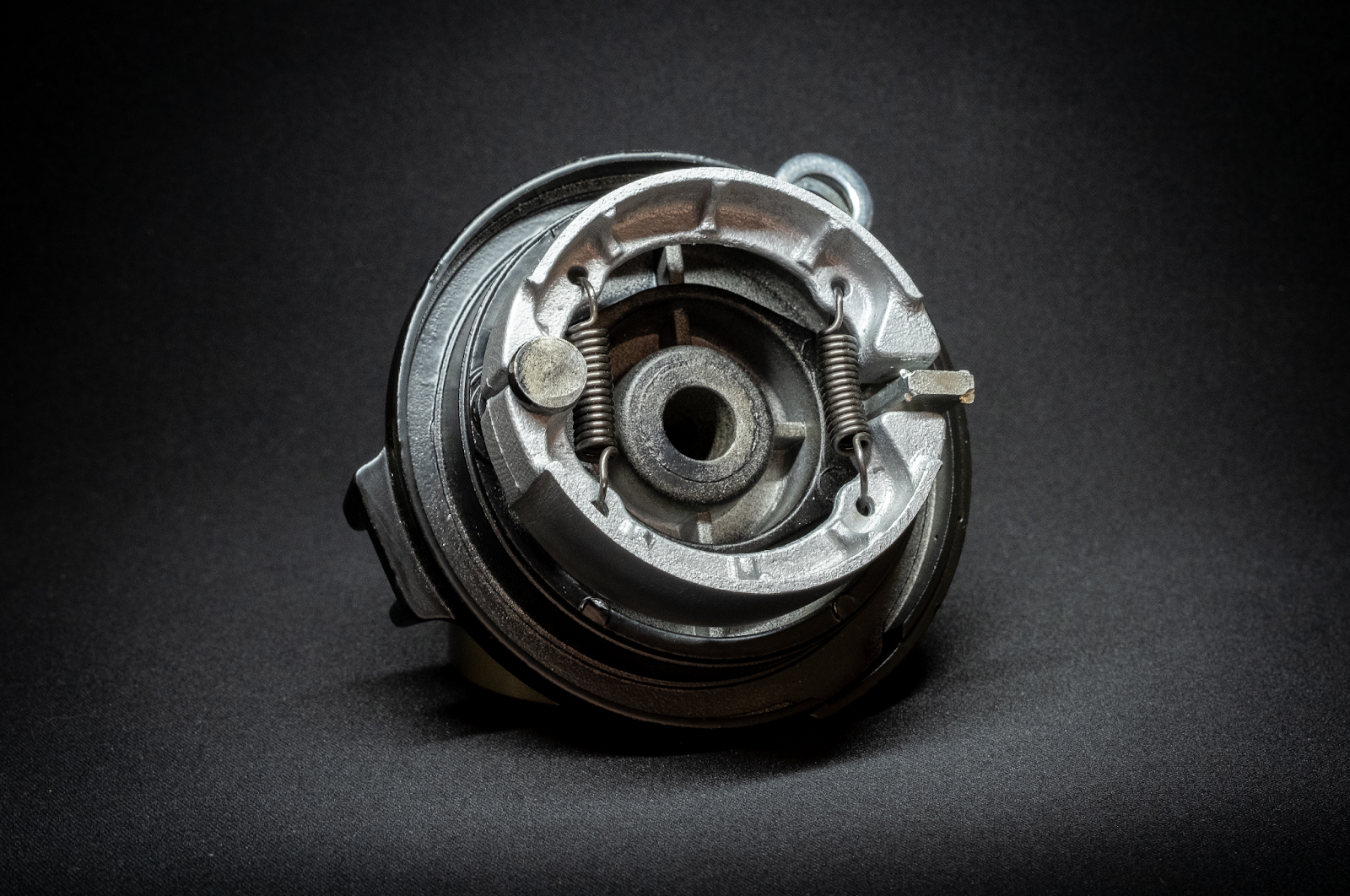
David and his small team have been highly efficient in developing the beta system, and we’re excited to support them as they emerge from stealth to work closely with automotive companies to redefine how products are developed.
And if you’re a Mechanical Engineer, Microwave Expert, Casting expert/metallurgist, software engineer or technician, join them! They’re hiring for a bunch of roles right now.